rotating bending fatigue|bending stress definition : trader A rotating-bending testing machine is comprised mainly of a motor to rotate the wire and a constraint to maintain the strain amplitude. Rotating-bending fatigue testing has become a common test setup for the structural fatigue evaluation of Nitinol wires (Tobushi et al., 1998). Resultado da 23 de fev. de 2024 · arrow_forward. Follow daily all liturgical journey of the Church through the Application Daily Liturgy. The application provides the .
{plog:ftitle_list}
WEBFunkytown. " Funkytown " is a song by American disco - funk group Lipps Inc., released by Casablanca Records in March 1980. It was written and produced by Steven Greenberg .
A rotating-bending testing machine is comprised mainly of a motor to rotate the wire and a constraint to maintain the strain amplitude. Rotating-bending fatigue testing has become a common test setup for the structural fatigue evaluation of Nitinol wires (Tobushi et al., 1998).Lightweight titanium alloys are being increasingly used in high value .
Fatigue test data from three different test methods — rotating bending, four-point .ADMET's Rotating Beam Fatigue system is a low cost table top unit ideal for generating data necessary for constructing S-N diagrams.
Lightweight titanium alloys are being increasingly used in high value structures, but in-depth knowledge of the rotating bending fatigue (RBF) mechanism remains insufficient, .Rotating Beam Fatigue testing allows researchers to perform fatigue testing at higher frequencies while saving capital expenses by purchasing a much simpler and more cost . In this video, we run a test on ADMET's Rotating Beam Fatigue Testing System. To see our updated Rotating Beam Fatigue system please click here: https://www..Isothermal rotating bending fatigue (IT-RBF) testing may simulate industrial components' high temperatures and rotating environments. This state-of-the-art review paper covers the current research on IT-RBF failure in wrought and .
Fatigue test data from three different test methods — rotating bending, four-point bending, and cantilever bending are evaluated. Comparison of the test data shows that, in .
A large-scale fatigue testing machine based on the rotating beam method in a four-point bending configuration was designed and built. With the device, high-strength metal .
This document specifies the method for rotating bar bending fatigue testing of metallic materials. The tests are conducted at room temperature or elevated temperature in air, the .Rotating beam fatigue testing is a mechanical test method used to evaluate the fatigue properties of materials. In this test, a beam specimen is subjected to cyclic loading, which induces repeated bending causing failure over time. In rotating beam fatigue testing applications, a bending stress is applied to a round specimen in constant rotation, causing the surfaces of the specimen see alternating tensile and compressive stresses. This method . Rotating beam
Fatigue fractures in rotary bending show a marked similarity to those arising from bending alone but there are important differences that generally enable the one to be distinguished from the other. G. Cylindrical bar subjected to a constant or fluctuating bending moment during rotation, with a change of section giving a moderate stress . In this study, rotating bending fatigue tests have been conducted for carbon fiber-reinforced epoxy composites. Hollow cylindrical specimens were prepared for two different lay-up sequences, i.e., [± 45°]2 and [± 45°/(90°)2] using filament winding process. These specimens were tested at constant stress levels with zero mean stress using an in-house built .Rotating Beam Fatigue Testing (ISO 1143 Metallic materials – Rotating bar bending fatigue testing) Rotating Beam Fatigue testing (sometimes referred to as the R.R. Moore method) has been around since the 1800s. It enables researchers to: Perform fatigue testing at higher frequencies, often up to 100Hz, leading to faster actionable data . The rotating bending fatigue test on aluminum alloys at high speed and high frequency up to 10 5 cycles by applying an applied load of 90% of elastic limit . Three specimens were able to test by increasing the stress level in a short, accelerated testing method. In two specimens tested above fatigue limit and drawn the S-N curve and another .
Although rotary bend wire fatigue is a relatively common test, the speed used to perform testing can vary greatly. Given that in vivo loading occurs at a much slower rate than the maximum speed of motors used in wire fatigue testers (e.g., approximately 72 beats per minute for cardiac loading versus 25,000 or more revolutions per minute (RPM) for a high-speed .E468/E468M-23a Standard Practice for Presentation of Constant Amplitude Fatigue Test Results for Metallic Materials . E2948-24 Standard Test Method for Conducting Rotating Bending Fatigue Tests of Solid Round Fine Wire . E3098-24 Standard Test Method for Uniaxial Pre-strain and Thermal Free Recovery of Shape Memory AlloysRotating Bending: The wheel spins while attached to a moment arm. Eccentric Mass: The wheel is stationary but an eccentric mass spins internally, creating a moment which allows the eccentric mass cornering fatigue to complete more than twice the amount of cycles in the same time as the rotating bending machine.

Our rotating beam fatigue line with bending moment capacities ranging from 60 in.-lb. to 1500 in.-lb. Details $ Call. Sheet & Plate Bending- Model VSS 40H. Utilizes a constant displacement method of loading and has a 40 lb. force capacity, with a maximum stroke of 2″ for flexural fatigue of metals, plastics and composites. . As stated and shown, there is a lack of experimental and analytical research on rotating bending (flexural) fatigue on 3D printed polymer material specimens, so the intention of the paper at hand was to address this issue with the introduction of rotating bending fatigue analysis of FFF specimens of PLA, ABS and ASA+ materials. Rotating bending fatigue (RBF) is the most effective method to simulate the alternating load on rotating blades, so it is often used for fatigue performance testing in the laboratory [9], [10]. Laser shock peening (LSP) is an attractive surface modification technology [11], .
ROTATING FATIGUE MACHINE. This machine demonstrates the fatigue failure of materials when subject to alternating stresses. Based on Wöhler’s design, it uses a motor to rotate a circular cantilever specimen with a load at its free end. It is in two parts: a robust main unit, and a separate control and instrumentation unit. .Most fatigue testing is conducted at the basic material level; differences between laboratory and service conditions must be considered by mechanical designers. Common test specimen types for obtaining fatigue data are shown in Figure 6. Figure 6 Fatigue Test Specimens: (a) Rotating Bending, (b) Cantilever Flat Sheet (cont.)
unidirectional bending fatigue
rotating bending fatigue testing machine
A rotating bending fatigue testing machine was developed by keeping in mind the basic concepts of technical theory of bending of elastic beams. Different specimens of 6mm to 8mm diameter of .
Gears are essential components used for transmitting power between noncoaxial rotating shafts (Ref 1,2,3).The typical failure modes are tooth-breaking, tooth wear, tooth bonding, and tooth surface pitting (Ref 4).The tooth (root) bending fatigue (TBF) is the most dangerous failure mode due to the repeated loading, which leads to the nucleation and .To meet test needs of various applications, Fatigue Dynamics offers rotating beam test machines in bending moment capacities ranging from 60 in.-lb. to 1500 in.-lb. Optional accessories include a high temperature furnace (up to .
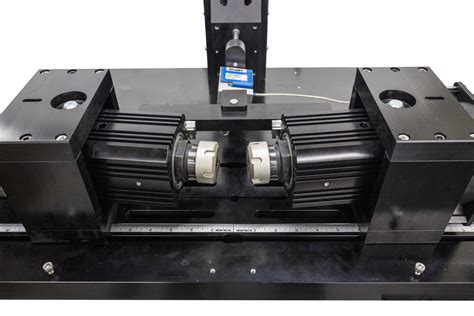
rotating bending fatigue machine
In this work, the rotating bending fatigue test was carried out on the laser direct energy deposited (L-DED) titanium alloy to simulate the service condition of the rotating blade, and the laser shock peening (LSP) post-processing was adopted to enhance the fatigue performance. The results showed that LSP induced gradient layer and phase .
bending stress reliability
In this video, we run a test on ADMET's Rotating Beam Fatigue Testing System. To see our updated Rotating Beam Fatigue system please click here: https://www.. This paper focuses on the effect of laser shock peening on the rotational bending fatigue life of S51740 stainless steel round bar specimens. The improvement of material properties by laser shock peening is investigated by combining simulation calculations and experiments. The main results are as follows: Finite element simulations yielded three sets of . The bending stresses can cause multiple fatigue initiation sites on each surface. Cracking progresses from both sides, typically meeting somewhere in the middle of the sheet thickness, depending on the symmetry of the bending. Rotating bending in notched shafts also can result in origins all around the shaft, with propagation toward the center . Some examples of plane and rotating bending fatigue diagnosis are shown in Photos 5 and 6. Photo 5 shows a 200 hp, 1180 RPM motor shaft that failed in less than a day. No progression marks means the fatigue load was constant. The instantaneous zone is relatively large, indicating the shaft was heavily loaded. Cracking started at numerous .
This paper presents the design and development of a fast rotating bending test machine f or high-cycle fatigue tests, which can rotate up to 18,000 rpm, generating cyclic s tresses at 300 Hz. The .
bending stress definition
The crack stable-jump propagation conditions of the material under rotating bending fatigue cropping are given. When the load meets the critical condition, that is 4 F L 2 a π (b-a) 3 = K fC Y, a sudden-jump propagation occurs. As K fc /Y has multiple values in the process of crack propagation, and multiple sudden-jump propagation occurs. It . Table 1 shows the experimental results obtained on rotating bending fatigue test machine. The experiment was conducted till the failure of composite specimen is observed as a fiber breakage or delamination of matrix. It has been observed from the results that, as the bending stress increases, the number of cycles to failure decreases. .An example of the effects of surface factors would be a typical rotating bending fatigue on a shaft like that in Figure 6. Machine toolmarks on the already small shaft radius increased the shaft stress concentration, which initiated a rotating bending fatigue failure. Figure 7: A corrected shaft radius, complete with a smooth surface finish
The rotating bending fatigue machine clamps the specimen as a cantilever, as shown in Figure 3. The test machine is TQ SM1090 (TecQuipment Ltd., Nottingham, UK) with versatile data acquisition system, which uses an adjustable dead weight for applying vertical, downward load on the specimen, using a self-aligning bearing inside a gimbal. .

4 de nov. de 2023 · Aqui você vai ver as fotos de Justin Bieber pelado, os nudes do OnlyFans de Tyler Posey, o ator Juliano Cazarré nu, Caio Castro, Jonas do BBB, .
rotating bending fatigue|bending stress definition